The Power of 3D Sand-Casting
The Solution for Depowdering –
4X Faster
Introducing
Now there’s a better way to depowder cores…Introducing ShotShower™ – ShotShower™ is an easy, simple and effective way to depowder cores and put profit back in your business.
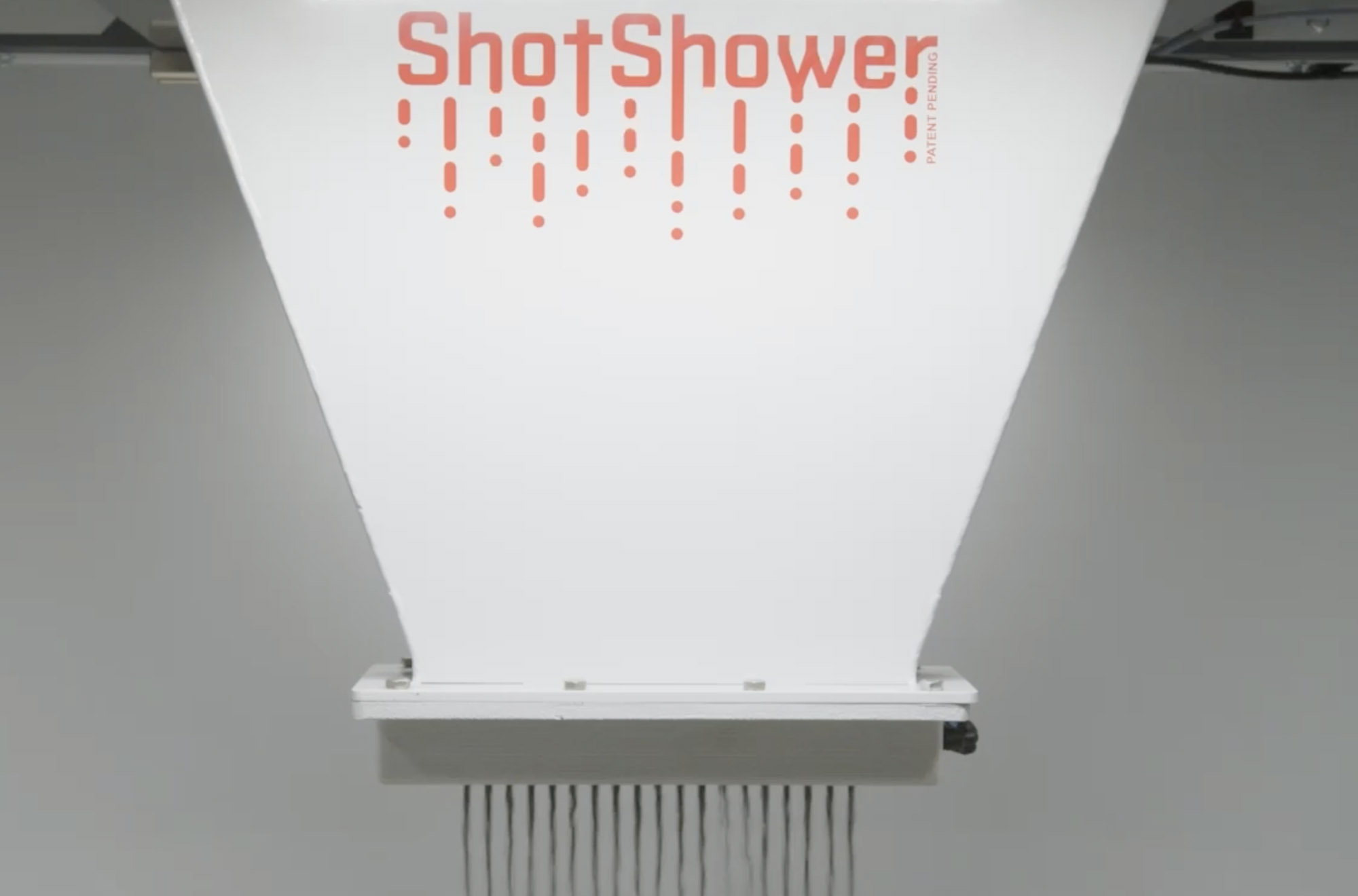
ShotShower™ Developed exclusively for 3-D Printed Cores
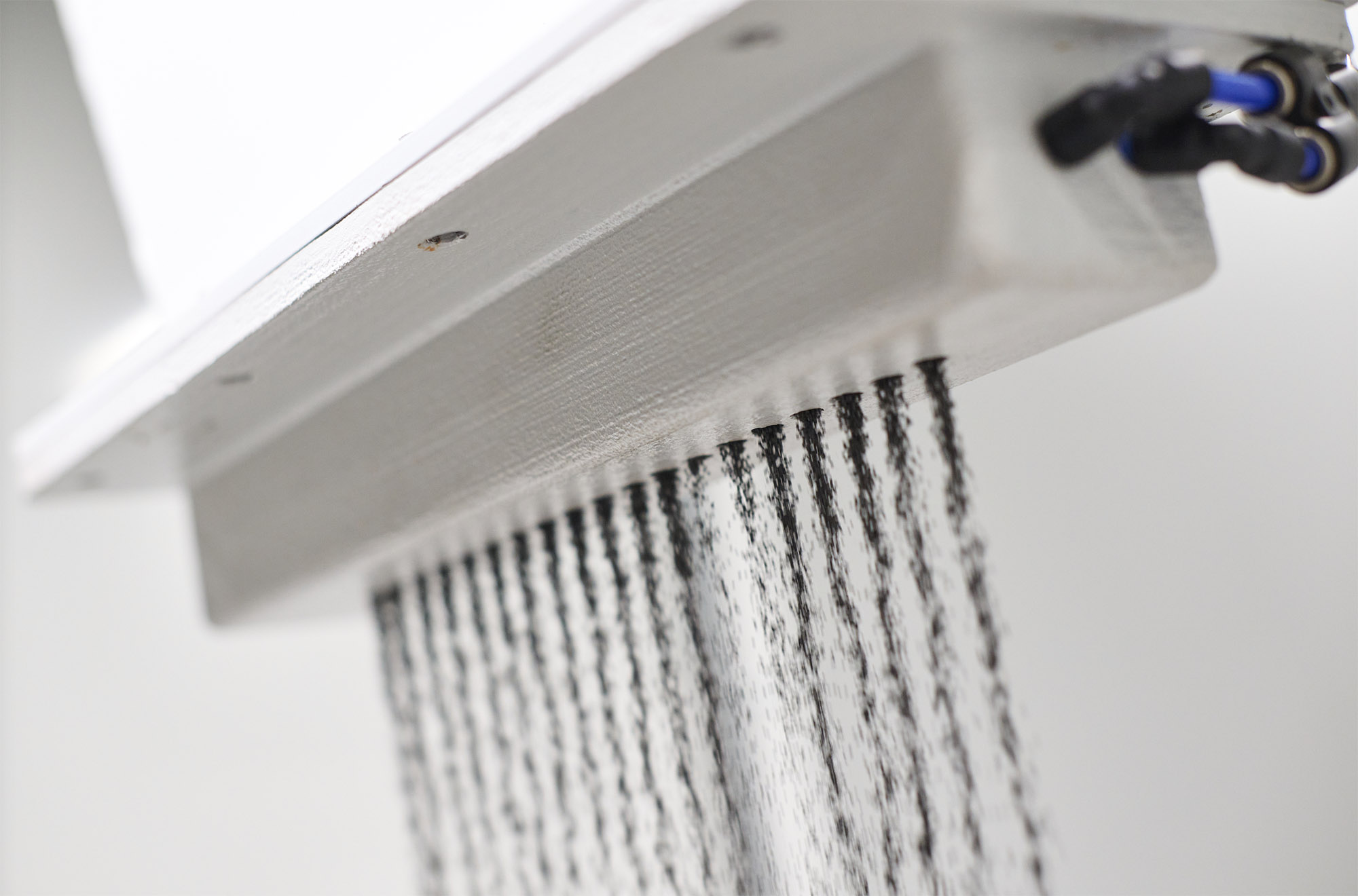
ShotShower™ Saves time and labor
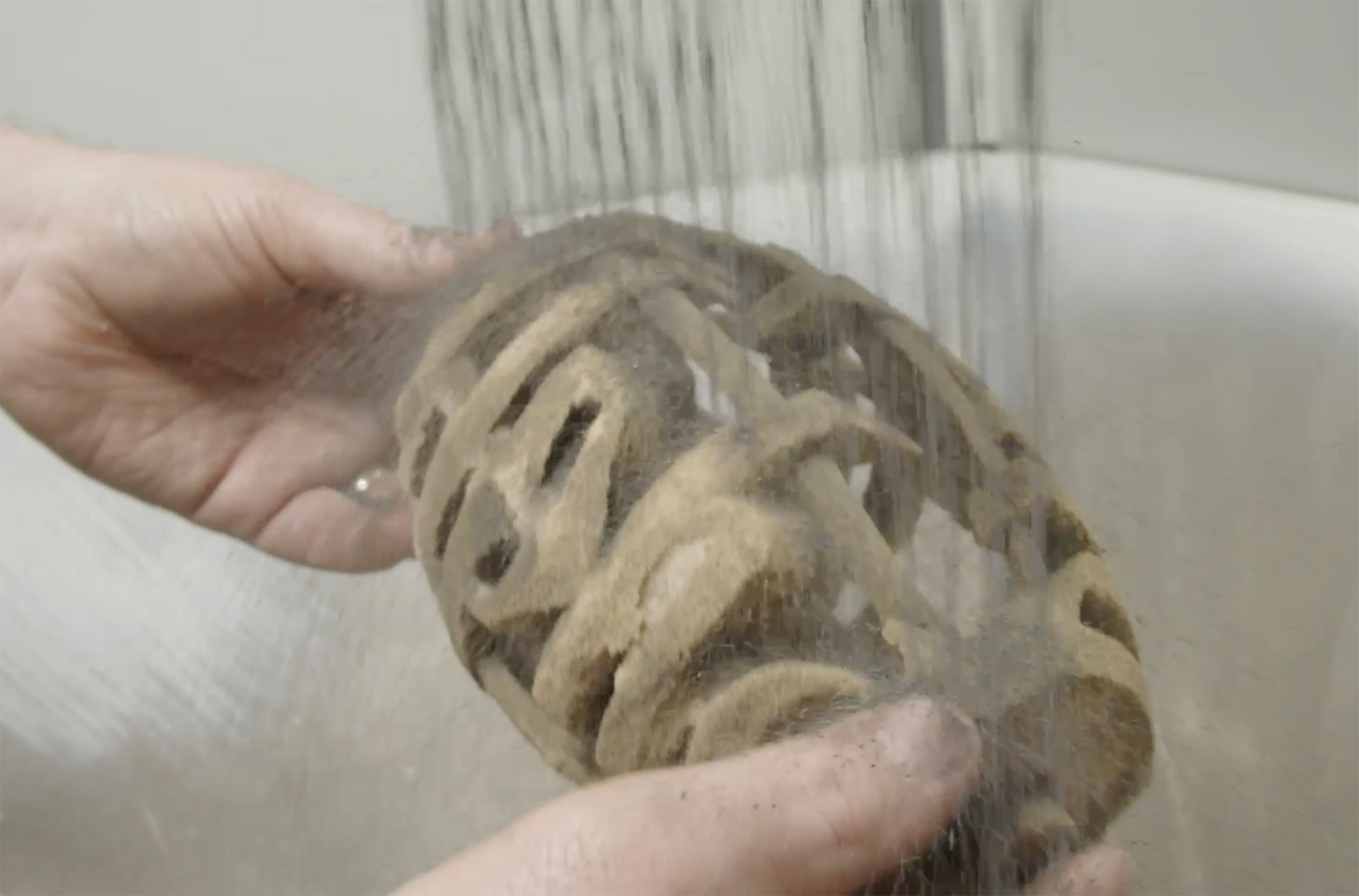
ShotShower™ Easy on your cores
Compare Standard 3-D Core Depowdering to ShotShower™
Handling 3-D printed cores can be difficult and time consuming. Intricate stems and narrow channels in the core design can easily fracture or break. IN fact, typically 5 out of 20 3-D printed cores will break during the cleaning or hand depowdering process (using a brush and compressed air).
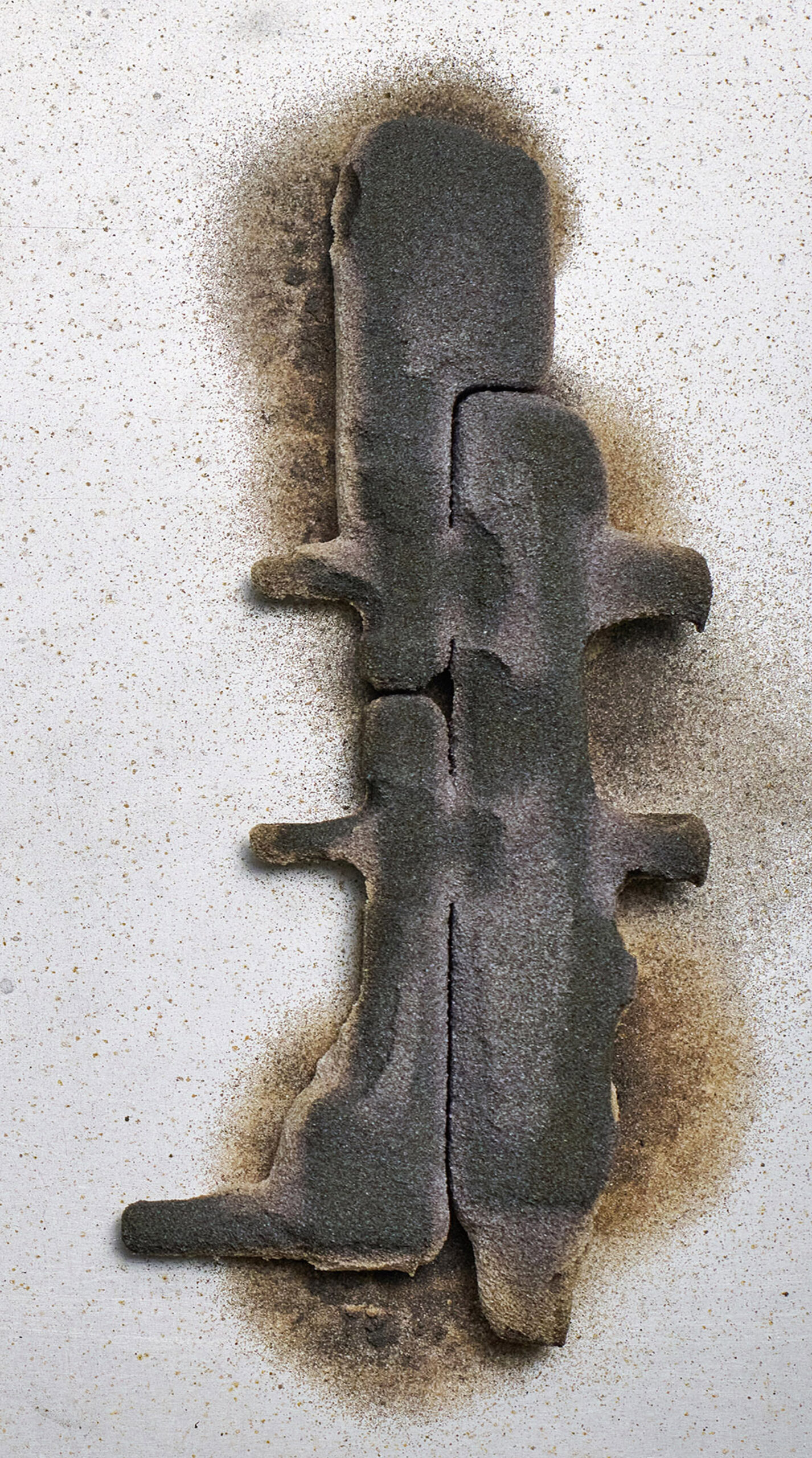
3-D Printed Core Ready for Depowdering
Handling 3-D printed cores can be difficult and time consuming. Intricate stems and narrow channels in the core design can easily fracture or break. Cores are typically depowdered using using a brush and compressed air.
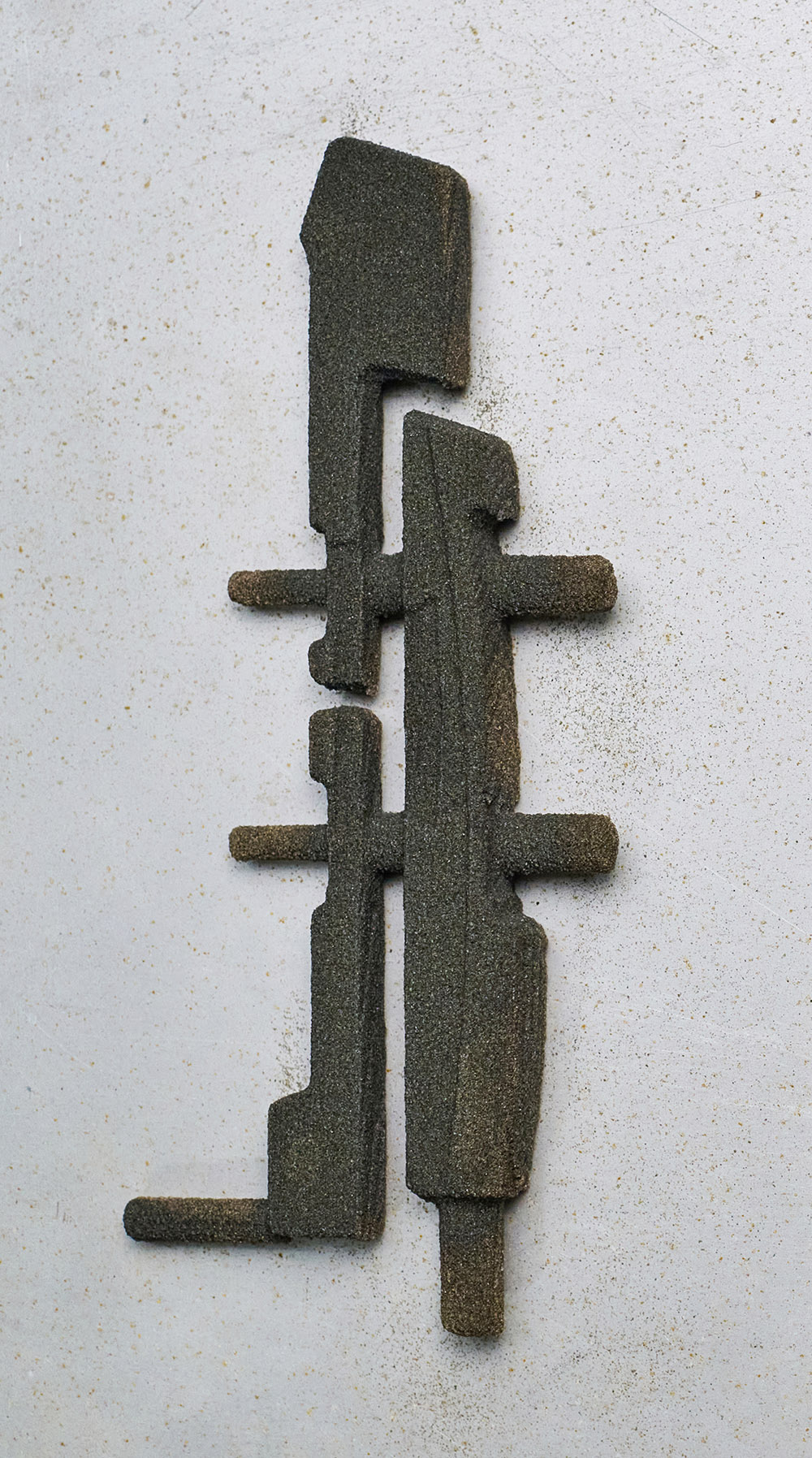
3-D Printed Core that has been Depowdered by hand
3-D printed cores depowdered by hand, done one after another, can retain some residue sand and be inconsistently cleaned. The typical hand cleaned unit takes several minutes. And if you are backed up in production and on a tight schedule, a core can receive a moderate cleaning.
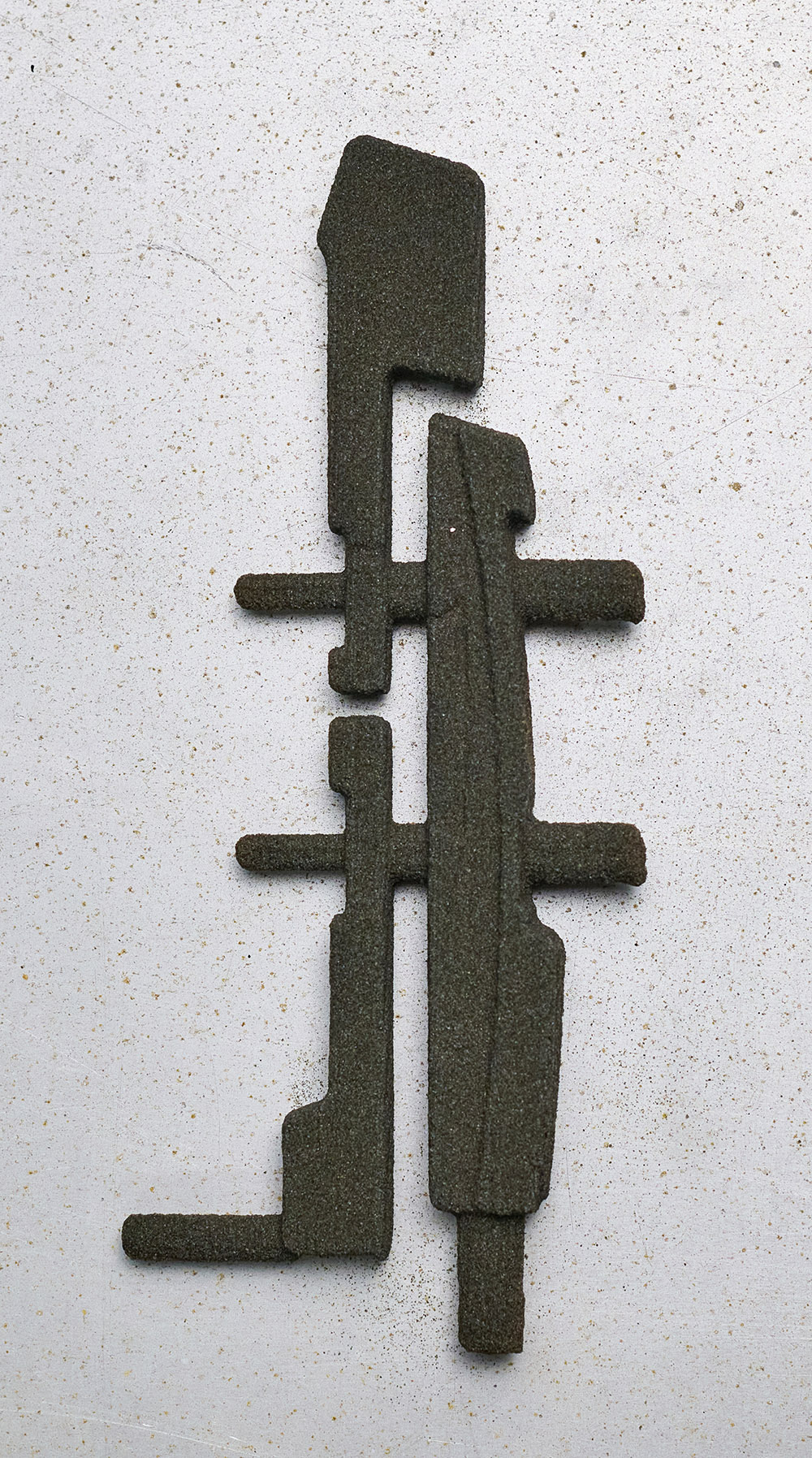
3-D Printed Core that has been cleaned with ShotShower™
3-D printed cores cleaned using ShotShower™ are perfectly cleaned (no lingering residue) in a dramatically shorter period of time, and with minimal or no breakage.
The Story Behind ShotShower™
Additive Manufacturing – The Rapidly Evolving Way to Make Parts
Since its inception in 1986, Additive Manufacturing (AM) has become a mature and refined method to make complex parts. Over the years, 3-D printing technology, sometimes referred to as stereolithography, has evolved to utilizing many materials such as polymers and powder metals.
Another facet of 3-D printing is its use in the foundry industry to make molds and cores. Of particular utility is using 3-D printing for fast prototyping or limited casting runs where production tooling costs could not be justified. This is especially true for complex geometries created in a Computer Aided Design (CAD) system, like Solidworks, that permit adjusting designs without scraping or reworking tooling and molds. It also offers the benefits of creating complex cores without the need to assemble several parts to make a complete core.
Current trends in using 3-D printing will continue to exert itself in the manufacturing arena and enable creating more and varied parts for the automotive, aerospace, medical and consumer goods markets. One area that needs addressing, if 3-D printing is to realize its full potential in the casting industry, is increasing core production efficiency and quality while minimizing the scrap rate and maximizing throughput so that it (core making) is not a bottleneck inhibiting the full use of casting capacity. Even with 3-D printing, the core making process requires depowdering to achieve a core ready for casting. Unfortunately, for many, the depowdering process is a major bottleneck that needs refinement to get away from manual depowdering operations that require a lot of operator skill, time and, most importantly, consistency in delivering final cores that are free from defects and meet customer needs and expectations.
In the casting world, its core production that needs its secondary operations, like depowdering, to advance so it can fully deliver the benefits 3-D printing provides.
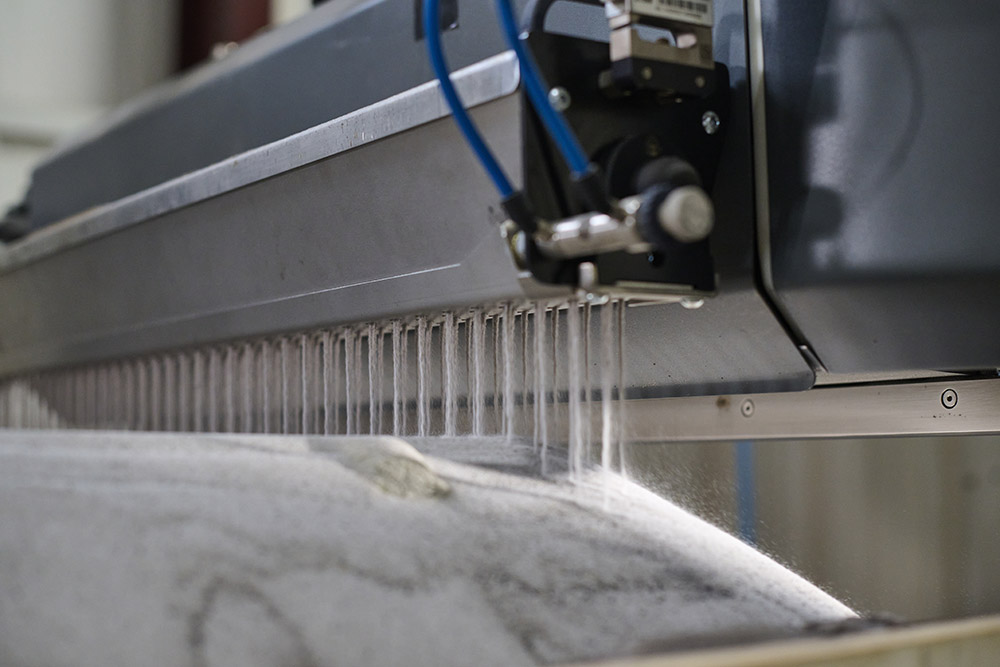
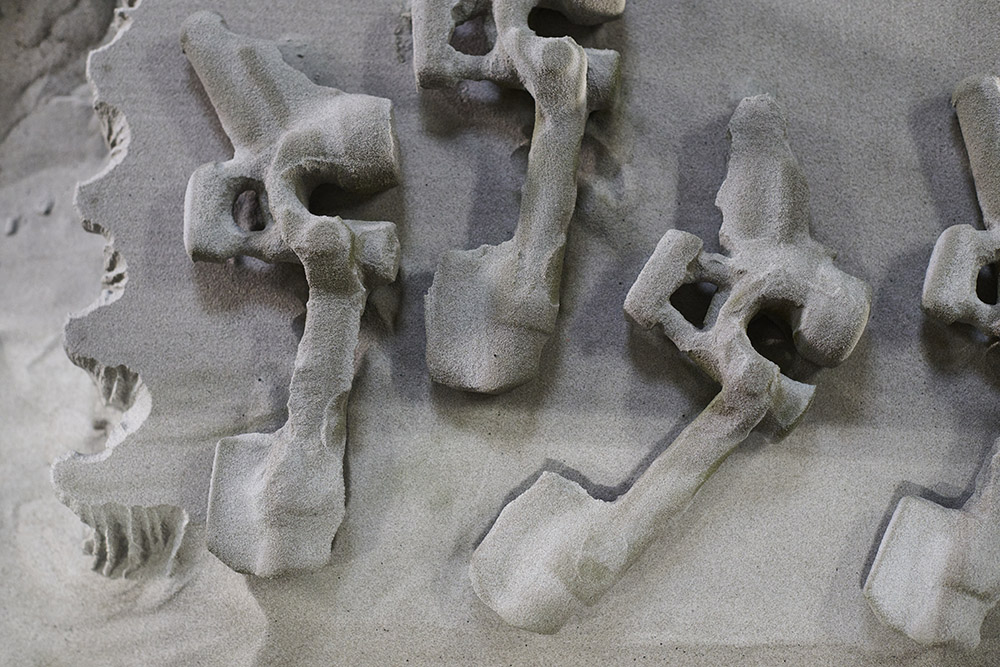
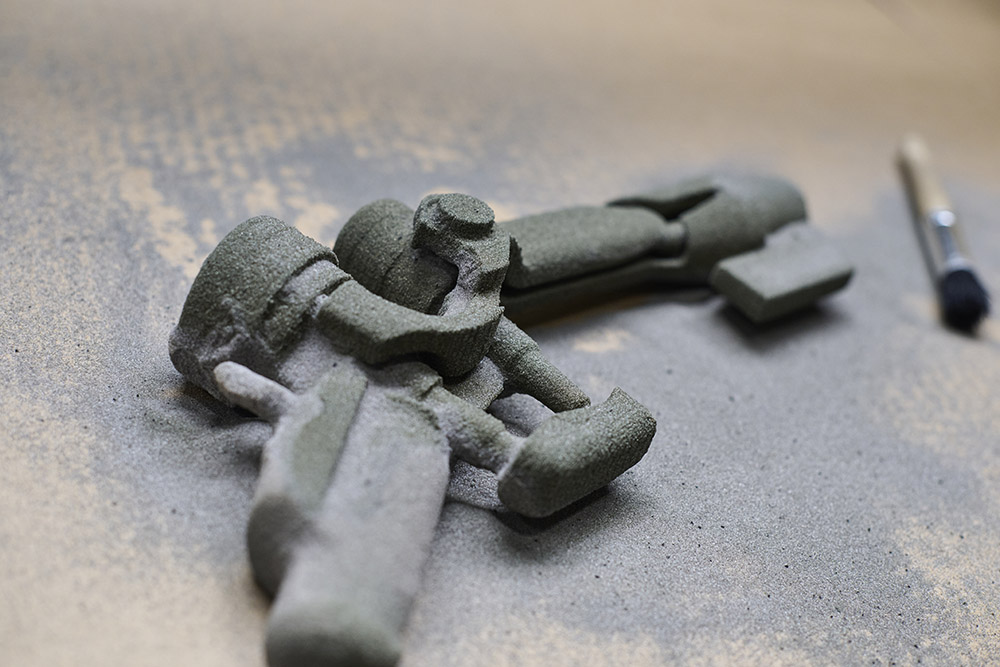
Depowdering – The Neglected 3-D Printed Core Making Step
Regardless of the binder when 3-D printing cores, the problem of removing the entrained core sand from the core’s final shape persists and presents a host of problems. Typically this secondary step in core making is accomplished by an operator using a soft brush and air nozzle to remove the entrained sand.
This method of depowdering presents several issues that affect core production:
- Operator skill; knowing how much pressure to apply so as to not disturb or alter the core’s shape or desired surface finish.
- Breakage; how good is the operator in successfully depowdering without creating a scrap that’s as high as 20% in many cases.
- Time; how quickly can the operator perform depowdering – assuming no breakage – and not become the bottleneck in core production.
- Processing delays; this is an issue with many binders when high heat and humidity are present. After the initial curing, the core needs depowdering before the entrained sand is also affixed to the core’s base geometry making it more difficult to create an acceptable core – requiring more time and effort with a good chance for increase in scrap.
If the operator can’t perform the depowdering task efficiently enough, the full benefit of the 3-D printing efficiency is diminished and maximum utilization of the capital equipment that’s the 3-D printing system is not realized.
Increasing automation in the depowdering phase is highly desirable to address the above issues. While manual operations will probably not be eliminated completely, the ability to quickly remove the majority of the entrained sand without excessive effort will help ensure greater throughput while reducing operator time per core and scrap.
Core Depowdering – Can the Process be Made Better
Removing the entrained sand from a 3-D printed core, or “depowdering,” is a major bottleneck in core production. Traditionally it’s a manual process involving soft brushes and air guns to remove the unwanted sand to produce an acceptable core. Manual depowdering raises many issues from operator skill, cycle time/throughput, quality and scrap. Automating the depowdering process can help deliver benefits not possible with a fully manual approach.
Utilizing automation, like the ShotShower™, can address the aforementioned issues. It’s gentle “shower” of fine shot efficiently removes sand from large areas in a single pass for faster throughput. The shot’s impact pressure in the depowdering process is easily adjusted by the distance the core is held from the shot dispensing chute with technique readily mastered by the operator in a fast, intuitive learning curve.
The ShotShower™’s predictable sand removing pressure greatly reduces the chances of damaging detailed and fragile core geometry to reduce scrap rates. It’s even capable of removing sand from numbers or lettering used for inconspicuous traceability data placed inside the casting’s cavities.
In actual use, ShotShower™ has proven it can depowder a 3-D print of 120 cores four times faster than traditional manual depowdering, This can enable the 3-D printer to be more fully utilized by more closely matching the speed of the depowdering with that of the printing process. It also resulted in reducing the scrap rate from 20% to 1% regardless of the much faster per-core depowdering cycle time.
Additionally, ShotShower™ only requires 120-vac power and low-pressure air supply. Plus it’s a compact unit that’s easily moved from one plant location to another. The shot is recovered and returned automatically to the dispensing chute while the sand is siphoned off for easy disposal.
While eliminating all manual depowdering operations is still in the future, ShotShower™ is a great leap forward towards improving and speeding the core depowdering process.
Casting – A Rapidly Changing Landscape
With regulations impacting casting operations and foreign competition eroding margins, the foundry that can rapidly adjust and adopt new technologies will be the survivor. Fortunately there’s been a recent recognition of the need to re-shore our manufacturing. The advantages are many, including quicker turn-around times, employment for many communities and the added security that come with the ability to control our own manufacturing destiny.
But simply wanting to re-shore is no guarantee of success. Foundries will continue to be required to meet regulations at the same time not being immune to the realities of competition in delivering a quality product at an acceptable cost to the customer.
Certainly, adopting lean manufacturing and six sigma along with other modern manufacturing methods will go a long way to increase efficiency and reduce waste. Another manufacturing element towards manufacturing efficiency is adopting the technologies that will speed up bottleneck operations while saving time, labor and reducing scrap rates.
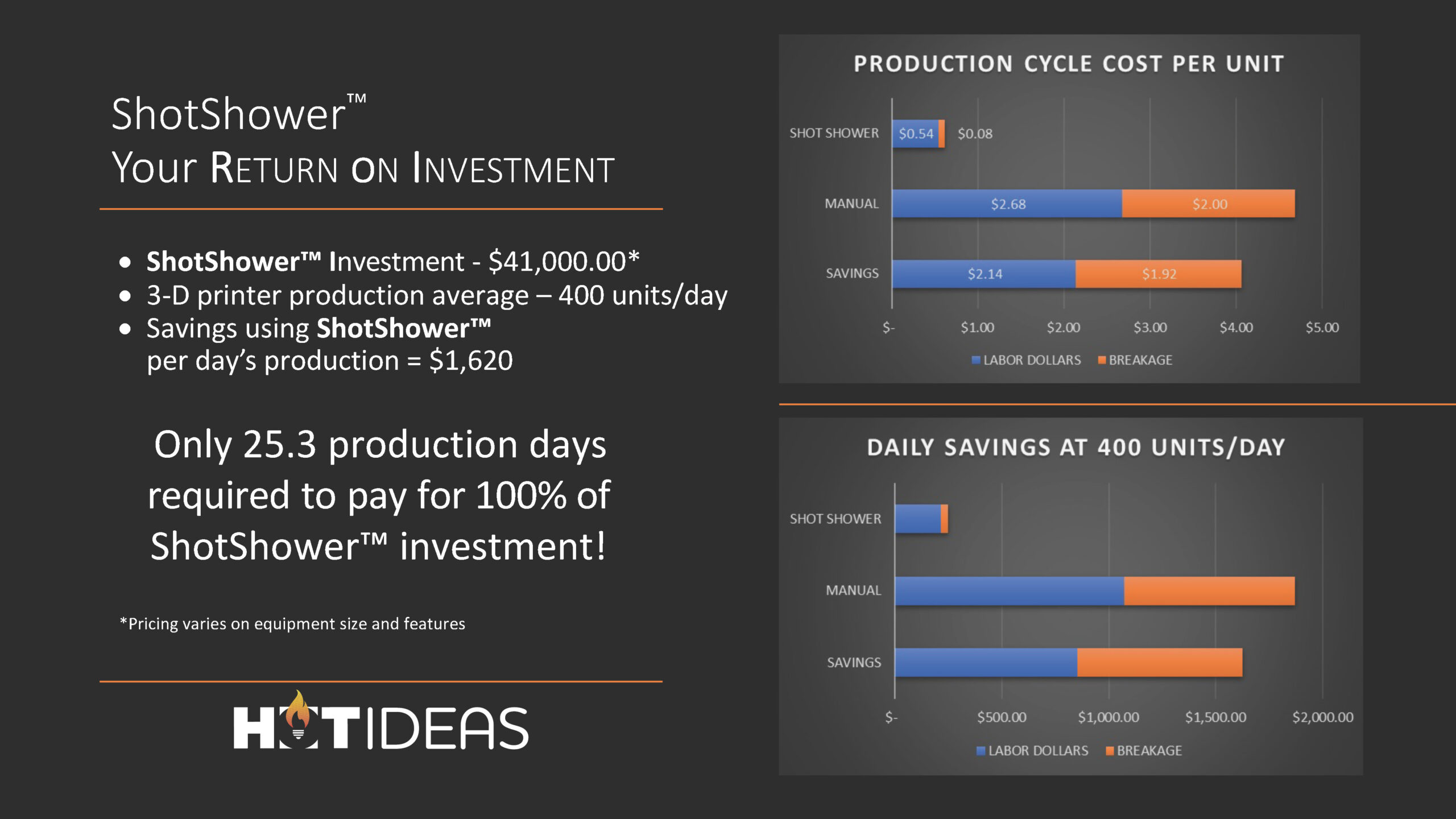
3-D core printing is one area that great strides have been made by greatly reducing or eliminating the need to assemble complex cores and increase the speed in which they’re made. But these gains can often be offset by manual depowdering operations that are time consuming, labor intensive and rely on a skilled operator to keep scrap rates low.
Fortunately, there’s ShotShower™ that can match the depowdering phase of core production with the speed of 3-D core printing. ShotShower™ can not only reduce labor costs, but increase quality and lower scrap rates…and free up employees for productive work elsewhere in your operations. While some look at a capital expenditure, like acquiring a Shot shower™, as a cost, it really is, in reality an investment in productivity, quality and competitiveness that will help ensure a foundry’s success. In short, ShotShower™ does not cost, it pays. Click this link to view a pro forma of ShotShower™ in an actual application.
The Big Picture –
Return on Investment Dynamics
- Reduction in labor when manual cleaning is eliminated
- Simplified operator training enables quick startup
- Full recovery of shot media and residual sand, separated for reuse
- Low cost of equipment maintenance
- Space saving footprint accommodates smaller work areas
- Mobile platform accommodates easy relocation
- Low cost and easily obtained cleaning media
- Full utilization of 3D printing production capacities
- Ability to produce more complex designs for casting
- Cores can be printed, cleaned and moved to casting in one piece versus multiples
- Sturdy design with minimal moving parts reducing points of failure
- Scalable machine design to handle small to medium fabrication parts
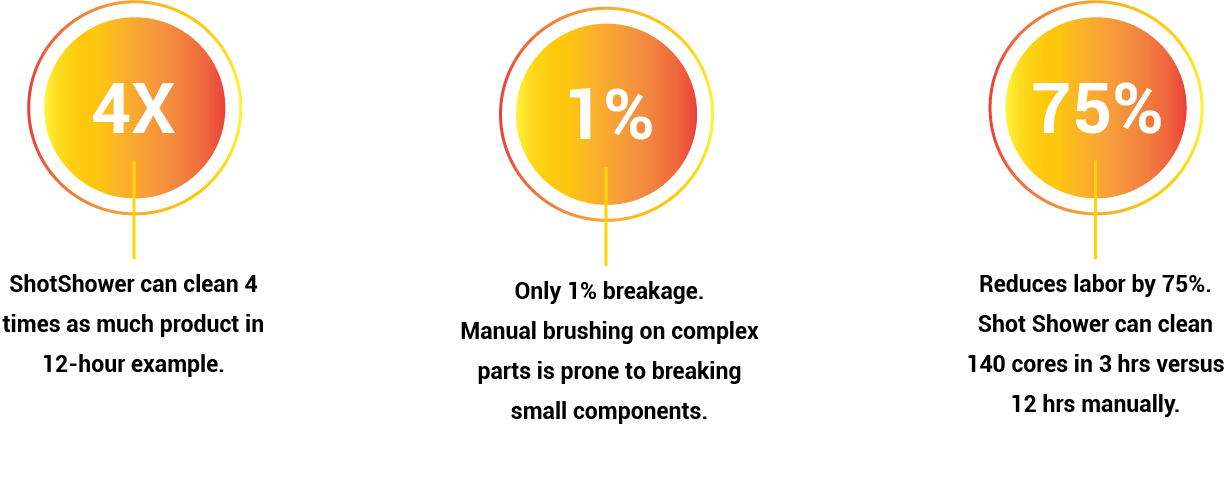
Meet the Innovators
As 3D printing for molds has become a regular mainstay for the foundry industry, so has the growing need to solve equipment and production problems, develop new ways to streamline labor involved and reduce cost of production. Their goal with any invention is to help foundrys save time, money, labor, and increase profitability.
Their most recent development – The ShotShower™ is just one example of their work. Trust us when we tell you, more HoT Ideas are on the way!